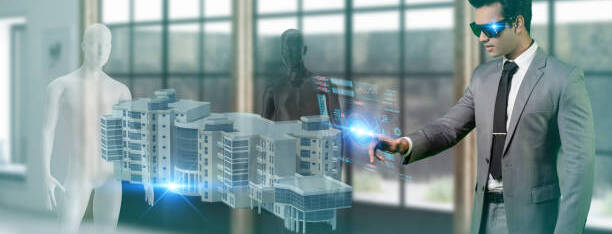
Digital Twins in Construction: Enhancing Cost Estimation and Project Management
In the realm of construction, where every project is a unique endeavor with its own set of challenges and uncertainties, the need for precision and efficiency in cost estimation and project management is paramount. The construction industry has historically grappled with cost overruns, delays, and unexpected issues that can significantly impact project timelines and budgets. However, a transformative technology has emerged to address these challenges head-on: digital twins. Digital twins are virtual replicas of physical assets or systems, and they are proving to be game changers in the construction industry. In this article, we will delve into the world of digital twins, exploring their application in construction and how they are enhancing cost estimation and project management.
The Genesis of Digital Twins
Digital twins are a product of the digital age, born out of advancements in computer technology, sensor networks, and data analytics. They enable the creation of a virtual representation of a physical object or system. This virtual counterpart mirrors the real-world entity in almost every aspect, collecting and updating data in real time to ensure its accuracy. Digital twins have found applications across various industries, from healthcare to manufacturing, but their potential in construction is particularly promising.
In the context of construction, a digital twin typically represents an entire project, including its physical infrastructure, systems, and even the surrounding environment. The digital twin is not a static model but a dynamic one, continuously fed with data from various sources such as sensors, drones, and project management software. This constant inflow of information ensures that the digital twin remains an accurate reflection of the physical project at all times. One of the primary goals of implementing digital twins in construction is to enhance cost estimation and project management.
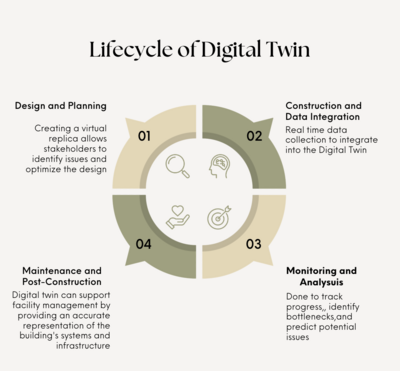
The Digital Twin Lifecycle in Construction
To fully appreciate the impact of digital twins on construction, it's essential to understand their lifecycle within a construction project.
The lifecycle of a digital twin in construction can be broken down into several key stages:
Design and Planning
At the inception of a construction project, architects, engineers, and designers create a digital twin that serves as the blueprint for the physical structure. This digital twin includes detailed 3D models, simulations, and relevant data about materials, cost estimates, and scheduling. By creating a virtual replica at this stage, stakeholders can identify potential issues and optimize the design for cost-efficiency and constructability.
Construction and Data Integration
As construction progresses, sensors and IoT devices are strategically placed throughout the construction site to collect real-time data. This data may include information about materials usage, equipment performance, weather conditions, and worker productivity. This information is then integrated into the digital twin, enriching it with up-to-the-minute insights into the project's status.
Monitoring and Analysis
Project managers and stakeholders can monitor the digital twin throughout the construction phase to track progress, identify bottlenecks, and predict potential issues. Advanced analytics and machine learning algorithms can process the data to provide valuable insights. For example, algorithms can predict when equipment maintenance is required, reducing downtime and costly delays.
Maintenance and Post-Construction
Once the construction is complete, the digital twin continues to serve a crucial role in maintaining and operating the building or infrastructure. Real-time data from sensors can help predict when maintenance is needed, extending the lifespan of the structure, and minimizing unexpected repair costs. Additionally, the digital twin can support facility management by accurately representing the building's systems and infrastructure.<p style="font-family: Calibri">
Transforming Cost Estimation
One of the most significant challenges in construction has always been accurate cost estimation. Many factors can lead to cost overruns, including unexpected delays, design changes, and fluctuating material prices. Accurate estimates are essential for securing funding, managing budgets, and ensuring a project's overall financial viability.
Digital twins are revolutionizing cost estimation in construction in several ways:
Realistic Design Validation
During the initial design and planning phase, digital twins allow for the creation of realistic 3D models that consider all aspects of the project, from architectural elements to structural integrity. By visualizing the project in detail, stakeholders can identify potential issues that might lead to cost overruns and address them before construction begins. This proactive approach significantly reduces the likelihood of unforeseen expenses.
Continuous Data Integration
As the construction progresses, data from the site, equipment, and materials are continuously integrated into the digital twin. This real-time data ensures that cost estimations remain accurate, even in the face of changing conditions. For example, if material prices increase suddenly, the digital twin can automatically update cost projections, allowing project managers to make informed decisions.
Risk Assessment and Mitigation
Digital twins enable construction teams to perform comprehensive risk assessments by simulating various scenarios. By running simulations based on real-time data, project managers can identify potential risks and their financial implications. This allows for the development of mitigation strategies to minimize the impact on the project's budget.
Resource Optimization
Digital twins can help optimize resource allocation. By analyzing data on equipment usage, labor productivity, and material consumption, project managers can identify inefficiencies and make adjustments to optimize resource allocation. This leads to cost savings and ensures that resources are used efficiently throughout the project.
Enhancing Project Management
Efficient project management is the cornerstone of successful construction projects. Digital twins are reshaping project management practices by providing real-time visibility and predictive capabilities:
Real-Time Progress Monitoring
Project managers can monitor the progress of a construction project in real-time through the digital twin. This visibility allows them to detect any deviations from the plan and address issues promptly. For instance, if a particular phase of construction is falling behind schedule, project managers can take corrective actions to bring it back on track, reducing delays and associated costs.
Communication and Collaboration
Digital twins facilitate collaboration among project stakeholders, including architects, engineers, contractors, and owners. All parties can access the digital twin and share information, making communication more efficient. This collaborative approach fosters better decision-making and reduces the likelihood of miscommunication that can lead to costly mistakes.
Predictive Analytics
Predictive analytics powered by digital twins offer project managers the ability to foresee potential problems before they escalate. For example, if data suggests that a particular piece of equipment is showing signs of wear and tear, the system can generate maintenance alerts, preventing costly breakdowns and project delays.
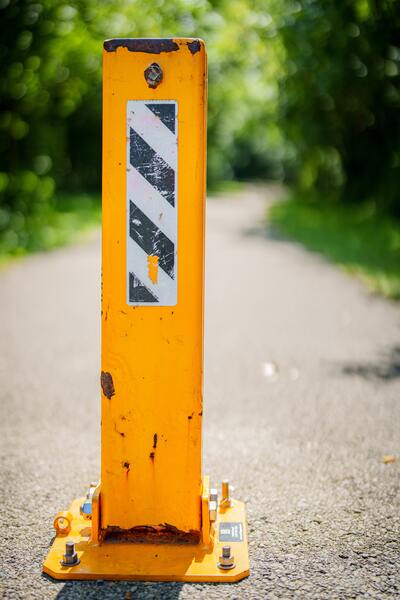
Safety Management
Safety is a paramount concern in construction, and digital twins can enhance safety measures. By analyzing data from sensors and cameras on the construction site, the digital twin can detect safety hazards and provide real-time alerts. This not only reduces the risk of accidents but also helps avoid costly litigation and delays associated with accidents.
Case Studies: Digital Twins in Action
To illustrate the transformative power of digital twins in construction, let's explore a couple of real-world case studies:
Hudson Yards, New York City, USA
Hudson Yards, one of the largest real estate developments in the United States, utilized digital twins throughout its construction. The project encompassed multiple skyscrapers, a shopping center, a cultural space, and a public plaza. Digital twins were employed to monitor the construction progress, coordinate complex logistics, and optimize resource allocation. As a result, Hudson Yards was completed on time and within budget, a remarkable achievement given its scale and complexity.
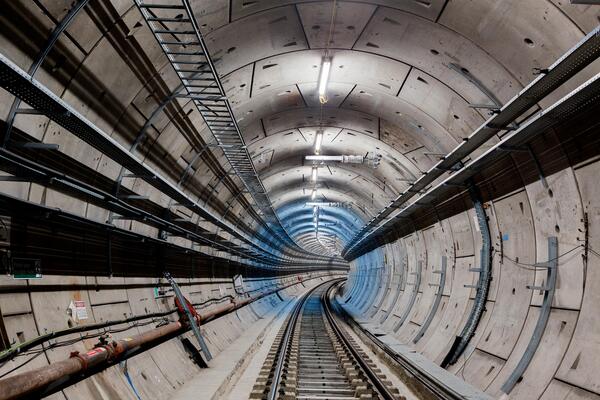
Crossrail, London, UK
Crossrail, a major rail project in London, faced numerous challenges, including tight schedules, complex underground construction, and the need to minimize disruptions to the city's existing infrastructure. Digital twins played a crucial role in planning and executing this massive project. They provided real-time insights into tunneling progress, monitored the condition of the underground structures, and helped manage the extensive network of sensors and systems. Crossrail was delivered on schedule and has set new standards for urban rail projects.
The Shard, London, UK
The Shard, an iconic skyscraper in London, utilized digital twin technology during its construction. Sensors and IoT devices were strategically placed throughout the building to monitor structural health, energy usage, and environmental conditions. This data was integrated into the digital twin, allowing for real-time monitoring of the building's performance. This enabled the facility management team to optimize energy efficiency, reduce operating costs, and ensure the building's long-term sustainability.
Challenges and Future Directions
While digital twins hold immense promise for the construction industry, they also present challenges that need to be addressed:
Data Integration
Integrating data from various sources into a cohesive digital twin can be complex. Robust data management systems are essential to ensure that the digital twin remains accurate and reliable.
Cost
Implementing digital twin technology can be costly, particularly for smaller construction firms. However, the long-term benefits often outweigh the initial investment.
Privacy and Security
Protecting the data collected by digital twins is essential. Construction companies must establish robust cybersecurity measures to safeguard sensitive information.
Skills and Training
The construction industry needs a workforce with the skills to create and manage digital twins. Training and education programs will play a pivotal role in bridging this skill gap.
In the future, we can expect digital twin technology in construction to become more accessible and sophisticated. Artificial intelligence and machine learning will further enhance predictive analytics, making cost estimation and risk management even more precise. As the technology evolves, it will become an integral part of construction project management, helping the industry become more efficient, sustainable, and cost-effective.
Conclusion
Digital twins are transforming the construction industry by offering dynamic virtual replicas of projects, enabling better cost estimation and project management. Through real-time data integration, predictive analytics, and enhanced communication, digital twins empower construction professionals to make informed decisions, optimize resource allocation, and proactively address issues. As the construction industry continues to embrace this technology, we can anticipate more efficient, sustainable, and successful construction projects in the future. The era of digital twins has arrived, and it is reshaping the way we build the world around us.
Check https://app.bidlight.com for how BidLight can help you estimate your BIM model!