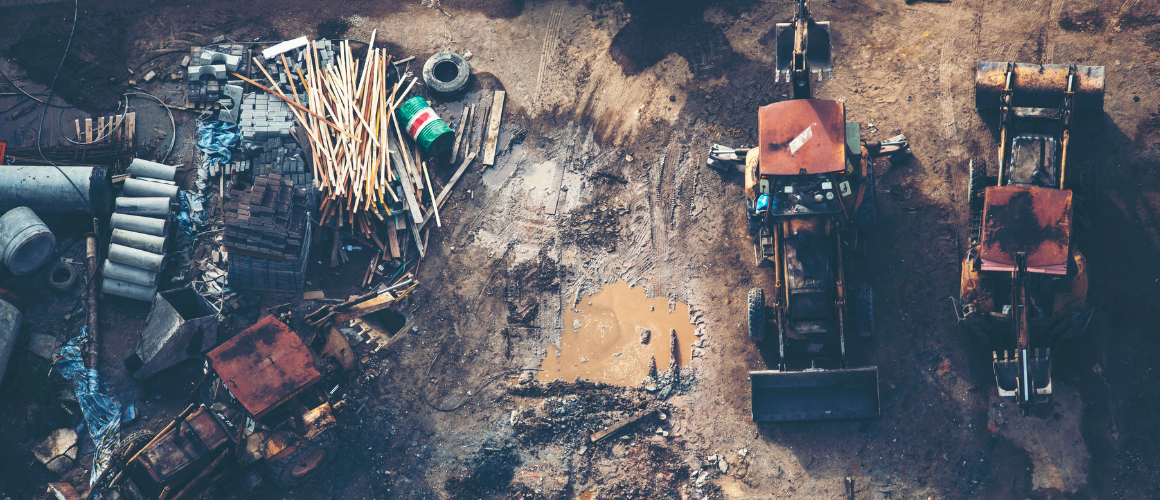
5 Construction Pitfalls & How BEP Solves Them
Are your construction projects often tangled in delays and cost overruns? If so, you're not alone. In the bustling world of construction, it’s easy to get caught in a web of complex processes and unforeseen challenges.
But here’s the thing: these problems are often not just bad luck or unavoidable circumstances. They might be signs that your current processes are failing you. Recognizing these signs is the first step towards turning things around.
In this blog, we’ll explore seven clear indicators that your construction processes might be hindering your projects and, ultimately, your business success. Don't worry, though; it's not all doom and gloom. We'll also introduce a game-changing solution: the BIM Execution Plan (BEP). This plan is not just a tool; it's a transformational approach that could reshape how you manage your construction projects.
So, let’s dive in and discover what these signs are and how BEP can help transform your challenges into triumphs.
Problem 1: Inconsistent Communication
First up on our list is something we've all faced: communication mishaps. In the construction world, where teams are often large and tasks are many, keeping everyone on the same page is crucial. But let's face it, this doesn’t always happen as smoothly as we'd like.
Have you ever been in a situation where crucial information got lost in translation? Maybe the architects didn’t get the memo about a design change, or the suppliers were unaware of a schedule shift. These aren’t just small hiccups. They can lead to serious project delays and cost overruns.
Inconsistent communication in construction projects is like trying to complete a puzzle with missing pieces. You might push forward, but the end result is never quite right. It leads to frustration, wasted time, and often, a compromised project quality.
Recognizing this issue is key. But more importantly, it's about understanding that it's not just about more communication; it's about better, more structured communication. This is where many processes fall short, and where the need for a robust solution becomes evident.
Problem 2: Overlooked Project Details
Now, let’s talk about the little things. In construction, details matter – a lot. But in the rush to meet deadlines and manage big-picture elements, these small but crucial details often get overlooked. And here's the tricky part: small mistakes can lead to big problems.
Picture this: a minor error in a measurement or a small oversight in material specifications. Seems insignificant, right? But in construction, such minor slips can snowball into major issues, causing rework, delays, and additional costs. It’s like a domino effect; one small misstep can knock everything off course.
These overlooked details can stem from various factors – rushed planning, miscommunication (as we discussed earlier), or simply the human tendency to focus more on the bigger picture. Whatever the reason, the result is the same: a project that’s not quite up to the mark.
Identifying these oversights early is crucial. It’s about having a process in place that pays attention to the minutiae, ensuring that every aspect of the project is double-checked and aligned with the overall plan. This level of meticulousness is often missing in traditional processes, but it’s essential for the success of any construction project.
Problem 3: Budget Overruns
Next, let's tackle a problem that makes everyone cringe: budget overruns. It's no secret that staying within budget is one of the biggest challenges in any construction project. How often have you started with a clear budget, only to see it spiral out of control as the project progresses?
Budget overruns can stem from various factors – unexpected changes in material costs, unforeseen issues on the site, or delays due to any number of reasons. But at the heart of many of these issues is a lack of proactive budget management and foresight in the planning stages.
It's like planning a road trip without considering potential detours or fuel costs. You might set out with a certain budget in mind, but without accounting for these variables, you're likely to spend more than you planned.
The impact of budget overruns goes beyond just financial strain. It can strain relationships with clients and stakeholders, tarnish your reputation, and even put the viability of the project at risk.
Recognizing the importance of accurate budget forecasting and ongoing financial management is crucial. It’s not just about setting a budget; it’s about continuously monitoring and adjusting it to align with the evolving dynamics of the project. This level of financial vigilance is often missing but is crucial for keeping your project in the green.
Problem 4: Delayed Timelines
Let's address a frustration familiar to many in construction: delayed timelines. In an industry where time is literally money, delays can be incredibly costly, not just in financial terms but also in terms of credibility and client trust.
Why do construction projects often run late? The reasons are many and varied. Sometimes it's due to unforeseen site conditions; other times, it's a result of delayed decisions or approvals, supply chain hiccups, or those pesky communication breakdowns we talked about earlier.
Picture the domino effect here: one delay in a critical task can push back the entire project schedule. It's like waiting for a delayed train. One late train can disrupt the schedule of all the trains that follow.
The impact of these delays is far-reaching. They can lead to increased costs, strained client relationships, and even legal issues in some cases. Plus, they can be a major stressor for everyone involved, from the project managers to the workers on the ground.
Acknowledging that delays are often a symptom of deeper issues in the project management process is the first step towards solving them. It's not just about working faster; it's about working smarter, with better planning, foresight, and flexibility built into your processes. This is where traditional methods often fall short and where a more innovative approach can make all the difference.
Problem 5: Low-Quality Outputs
Moving on to another critical issue: low-quality outputs. In the construction industry, the quality of your work is your signature. It's what sets you apart. But, when processes are haphazard or corners are cut, the end result often suffers – and so does your reputation.
Low quality can manifest in many forms: structural issues, poor finishes, non-compliance with standards, or even safety concerns. It's like baking a cake with the wrong ingredients; no matter how good it looks on the outside, the taste won’t meet expectations.
So, what leads to these quality issues? Often, it's a combination of rushed timelines, inadequate skills or oversight, and sometimes, the use of subpar materials. It's also about the lack of a cohesive quality control process that monitors every stage of construction.
The consequences of low-quality work are not just cosmetic. They can lead to costly rework, legal liabilities, and a loss of trust from clients and the public. And in an industry where reputation is everything, this can be a hard hit to recover from.
Quality in construction is non-negotiable. It’s about pride in your work and delivering a product that stands the test of time. Recognizing the importance of consistent quality control and the need for processes that ensure excellence at every turn is key to overcoming this challenge.
As we wrap up, it’s clear that the challenges in the construction industry – inconsistent communication, overlooked project details, budget overruns, delayed timelines, and low-quality outputs – are not just individual issues. They are interconnected problems that can significantly impact the success and reputation of your construction projects and business.
But here's the good news: each of these challenges presents an opportunity for transformation. This is where the BIM Execution Plan (BEP) comes into play. BEP isn't just a tool; it’s a comprehensive approach that addresses each of these problems head-on. By integrating BEP into your projects, you’re not just solving individual issues; you’re overhauling your entire project management process for the better.
Adopting BEP is more than just a step towards better project management; it’s a leap towards transforming how you conduct your construction business. It’s about building a legacy of efficiency, reliability, and excellence.
So, as you move forward in your construction journey, consider the power of BEP in turning your challenges into triumphs. Embrace the change, and watch as your projects – and your business – reach new heights of success.